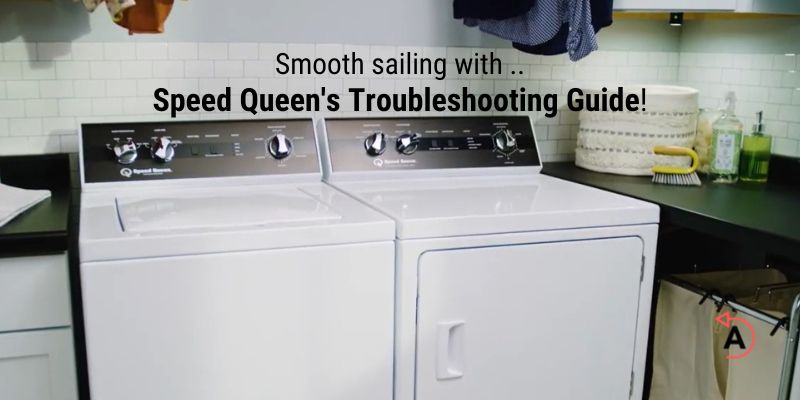
Looking for Speed Queen Dryer Troubleshooting Guide: Expert Tips to help you troubleshoot and resolve common issues with your Speed Queen dryer? You’ve come to the right place!
In this guide, we provide expert tips and step-by-step instructions to ensure efficient and hassle-free drying performance.
“Empower yourself with our expert insights for hassle-free dryer troubleshooting.”
Introduction
When it comes to household appliances, a reliable and efficient dryer is essential for ensuring your laundry is dried quickly and effectively.
Speed Queen dryers are known for their durability and performance, but like any appliance, they can experience issues from time to time.
In this troubleshooting guide, we will explore common problems that you may encounter with your Speed Queen dryer and provide you with practical solutions to get it back up and running smoothly.
Types of Speed Queen Dryers
Speed Queen offers a range of dryers to meet various laundry needs. Here are some types of Speed Queen dryers:
Electric Dryers: These dryers operate on electricity and are commonly found in residential settings. They offer efficient drying performance and are compatible with standard electrical outlets.
Gas Dryers: Gas dryers use natural gas or propane as a fuel source for heat generation. They are known for their faster drying times and cost-effectiveness in areas with lower electricity rates.
Stacked Dryers: Speed Queen also offers stacked dryer units that combine a washer and dryer into a single space-saving unit. These are ideal for compact laundry areas or locations with limited floor space.
Commercial Dryers: Speed Queen manufactures robust and durable dryers specifically designed for commercial use. These dryers are built to withstand heavy-duty laundry demands in laundromats, hotels, and other commercial settings.
Coin-Operated Dryers: Speed Queen produces coin-operated dryers, allowing businesses to offer laundry services to customers for a fee. These dryers are equipped with coin mechanisms and offer secure and convenient operation.
Note: It’s important to note that the availability of specific types may vary depending on your location and the model lineup offered by Speed Queen.
For detailed information and to explore the specific features of each dryer type, it’s recommended to visit the Speed Queen website or contact a local Speed Queen dealer.
Popular Models of Speed Queen Dryers
Here are 20 popular models of Speed Queen dryers:
- Speed Queen DR3000WE
- Speed Queen DR5000WE
- Speed Queen DR7000WE
- Speed Queen DR7000WG
- Speed Queen DR7003WE
- Speed Queen DR7003WG
- Speed Queen DR7EE3WE
- Speed Queen DR7EE3WG
- Speed Queen DR7EE7WE
- Speed Queen DR7EE7WG
- Speed Queen DR7EF1WE
- Speed Queen DR7EF1WG
- Speed Queen DR7EF2WE
- Speed Queen DR7EF2WG
- Speed Queen DR7EG0WE
- Speed Queen DR7EG0WG
- Speed Queen DR7EG2WE
- Speed Queen DR7EG2WG
- Speed Queen DR7EG3WE
- Speed Queen DR7EG3WG
Please note that the availability of specific models may vary depending on the region and the latest offerings from Speed Queen.
It’s recommended to visit the Speed Queen website or consult a local Speed Queen dealer for the most up-to-date and accurate information on available models.
Common Damaged Parts
The following are some common parts of a Speed Queen dryer that can become damaged over time:
Heating Element: The heating element is responsible for generating heat to dry your clothes. It can wear out or break, leading to a dryer that doesn’t produce enough heat or no heat at all.
Thermal Fuse: The thermal fuse acts as a safety device to protect the dryer from overheating. If it blows due to excessive heat, it will need to be replaced to restore normal operation.
Drum Belt: The drum belt is responsible for rotating the drum of the dryer. Over time, it can stretch, fray, or snap, causing the drum to stop spinning or create unusual noises.
Door Switch: The door switch is designed to stop the dryer from operating when the door is open. If the switch becomes faulty, it may prevent the dryer from turning on or starting a drying cycle.
Motor Bearings: The motor bearings allow the dryer drum to spin smoothly. Over time, they can wear out, resulting in a dryer that makes excessive noise during operation.
Control Board: The control board, also known as the main electronic control, is responsible for managing the dryer’s functions and settings. If it malfunctions or becomes damaged, it can cause various operational issues.
Thermistor: The thermistor is a temperature sensor that helps regulate the dryer’s heat levels. A faulty or damaged thermistor can lead to inaccurate temperature readings and improper drying.
Lint Filter: While not a part of the dryer itself, the lint filter can become damaged or clogged with lint over time. A damaged or excessively dirty lint filter can impede airflow and affect drying efficiency.
Keep in mind that the specific parts and their susceptibility to damage may vary depending on the model and age of your Speed Queen dryer.
If you encounter any issues with your dryer, it’s recommended to consult the dryer’s manual or contact Speed Queen customer support for assistance in identifying and replacing the damaged parts.
Regular maintenance, proper usage, and timely repairs can help prolong the lifespan of your Speed Queen dryer and ensure optimal performance.
“Looking for genuine Speed Queen dryer parts at best prices? Visit Repair Clinic for a wide selection of high-quality replacement parts”
Common Problems with Seppd Queen Dryer
- Dryer Not Turning On
- No Heat
- Uneven Drying
- Excessive Noise
- Overheating
- Lint Buildup
- Inaccurate Timer
- Door Issues
- Burning Smell
- Clothes Coming Out Wrinkled
- Electrical Problems
- Drum Not Spinning
- Gas Dryer Not Igniting
- Error Codes
- Regular Maintenance
“Get expert advice and ensure a seamless repair process. Keep your dryer running smoothly – visit Repair Clinic today!“
Speed Queen Dryer Troubleshooting Guide
In the Speed Queen Dryer Troubleshooting Guide, we will walk you through step-by-step solutions to common problems that may arise with your Speed Queen dryer.
From error codes to maintenance tips, this guide will help you troubleshoot and resolve issues to keep your dryer running smoothly.
Dryer Not Turning On
If you’re facing the frustrating issue of your Speed Queen dryer not turning on, don’t worry. There are a few troubleshooting steps you can take to identify and potentially resolve the problem.
Follow these simple suggestions to get your dryer up and running again:
Check the Power Connection: Start by ensuring that the power cord is securely plugged into the electrical outlet. Sometimes, due to movement or accidental disconnection, the cord may become loose. Firmly insert the plug into the outlet and give it a gentle tug to ensure it’s snugly connected.
Verify the Power Supply: Next, check the circuit breaker or fuse box in your home. A tripped breaker or blown fuse can cause the dryer to lose power. Locate the breaker or fuse corresponding to the dryer’s electrical circuit and reset or replace it if necessary. If you’re unsure which breaker or fuse is associated with the dryer, consult the electrical panel diagram or contact a professional electrician.
Inspect the Door Switch: The door switch is an important safety feature that prevents the dryer from operating when the door is open. If the door switch is not engaging properly, it can prevent the dryer from turning on. Open and close the dryer door a few times while paying attention to any clicking or resistance from the switch. If you notice any issues, the door switch may need to be replaced. Contact a qualified technician or Speed Queen customer support for assistance.
No Heat
If your Speed Queen dryer is running but not producing any heat, it can be frustrating and hinder your laundry routine. However, there are a few troubleshooting steps you can take to address this issue.
Follow these simple suggestions to identify and potentially resolve the “no heat” problem:
Check the Heat Setting: Ensure that the dryer’s heat setting is appropriately selected. Sometimes, the dryer may be set to a “no heat” or “air fluff” option, which doesn’t generate heat. Adjust the setting to a temperature that suits your drying needs.
Clean the Lint Filter: A clogged lint filter can restrict airflow and lead to poor heating performance. Before each use, make it a habit to clean the lint filter thoroughly. Remove any lint buildup by gently brushing or rinsing the filter under running water. Allow it to dry completely before reinserting it into the dryer.
Inspect the Venting System: A blocked or obstructed venting system can also cause a lack of heat in the dryer. Check the dryer’s exhaust vent, ductwork, and external vent cap for any obstructions such as lint, debris, or even bird nests. Clear away any blockages to ensure proper airflow.
Verify the Heating Element: The heating element is responsible for generating heat in the dryer. If it’s faulty or damaged, the dryer may not produce any heat. Consult your dryer’s user manual or contact Speed Queen customer support for instructions on how to inspect and test the heating element. If necessary, replace the heating element with a compatible one.
Check the Power Supply: Ensure that the dryer is receiving adequate power supply. Make sure the power cord is securely plugged into the electrical outlet and that the circuit breaker or fuse associated with the dryer’s electrical circuit is not tripped or blown. Reset or replace the breaker or fuse if needed.
Uneven Drying
If you’re experiencing issues with your Speed Queen dryer where your clothes are coming out damp or unevenly dried, there are a few troubleshooting steps you can take to address the problem:
Avoid Overloading: Overloading the dryer can prevent proper airflow and result in uneven drying. Make sure you’re not filling the dryer beyond its recommended capacity. Allow enough space for the clothes to tumble freely and circulate air effectively.
Check Venting System: A clogged or restricted venting system can hinder the dryer’s performance. Inspect the vent hose and ensure it’s not kinked, crushed, or clogged with lint or debris. Additionally, check the outside vent cover for any obstructions. Clear any blockages to allow for proper airflow.
Level the Dryer: An unbalanced or tilted dryer can cause clothes to bunch up and dry unevenly. Ensure that your Speed Queen dryer is level by adjusting the leveling feet. Use a level tool to check the alignment and make necessary adjustments.
Select the Right Dryness Level: Some Speed Queen dryers offer different dryness levels, such as “Normal,” “Delicate,” or “Extra Dry.” Make sure you’re selecting the appropriate setting for your load. Using a lower heat setting for delicate items or a higher setting for heavier fabrics can help achieve more consistent drying results.
Excessive Noise
If you’re experiencing excessive noise coming from your Speed Queen dryer, it can be quite bothersome. However, there are a few simple troubleshooting steps you can take to address this issue:
Inspect the Drum Bearings: Worn-out drum bearings are a common cause of noisy dryers. To check if this is the problem, manually rotate the drum with your hand. If you hear a grinding or squealing sound, it’s likely that the drum bearings are worn and need to be replaced. Contact a professional technician to assist with this repair.
Tighten Loose Screws or Bolts: Over time, the vibrations generated during dryer operation can cause screws or bolts to become loose. Carefully inspect the dryer’s interior and tighten any loose screws or bolts using the appropriate tools. This simple step may help reduce the noise significantly.
Remove Foreign Objects: Sometimes, objects such as coins, buttons, or small pieces of debris can find their way into the dryer drum, causing rattling or clanging noises. Turn off the dryer and inspect the drum thoroughly. Remove any foreign objects you find, ensuring that nothing is interfering with the smooth rotation of the drum.
Overheating
If you notice that your Speed Queen dryer is becoming excessively hot, it’s important to address the issue promptly to prevent potential damage and ensure safe operation. Below are some simple troubleshooting steps to tackle the problem of overheating:
Check Ventilation: Start by inspecting the dryer’s venting system. Make sure the vent hose is not kinked, clogged, or obstructed in any way. A restricted airflow can cause the dryer to overheat. Remove any lint or debris from the vent hose and the exterior vent opening.
Clean the Lint Filter: A clogged lint filter can restrict airflow and lead to overheating. Clean the lint filter before or after each use. Remove any lint accumulation by gently brushing or rinsing it under running water. Allow the filter to dry completely before placing it back in the dryer.
Avoid Overloading: Overloading the dryer can impede proper airflow, causing it to overheat. Ensure that you’re not putting too many clothes or bulky items into the dryer at once. Follow the manufacturer’s guidelines regarding load capacity.
Check Thermostat Functioning: The cycling thermostat and high-limit thermostat are safety features that regulate the dryer’s temperature. If they malfunction, the dryer may overheat. Consult the user manual or contact Speed Queen customer support for guidance on checking and testing the thermostats. Replace any faulty thermostats as necessary.
Inspect Heating Element: A faulty heating element can cause the dryer to overheat. If you’re comfortable working with electrical components, you can check the continuity of the heating element using a multimeter. However, it’s recommended to seek professional assistance for this task to ensure safety and proper diagnosis.
Lint Buildup
Lint buildup is a common issue that can affect the performance and efficiency of your Speed Queen dryer. It not only reduces drying effectiveness but also poses a fire hazard.
To prevent lint buildup and keep your dryer running smoothly, follow these simple troubleshooting steps:
Clean the Lint Filter: Before or after each use, clean the lint filter. Locate the lint filter, which is usually located on the top of the dryer or inside the dryer door. Remove any lint accumulated on the filter by gently sliding your fingers or a soft brush across the screen. Dispose of the lint in a trash bin. Regularly cleaning the lint filter helps maintain proper airflow and drying efficiency.
Inspect the Venting System: Periodically inspect the venting system to ensure it is free from lint buildup. Start by disconnecting the dryer from the power source. Then, detach the vent hose from the back of the dryer. Use a vacuum cleaner or a lint brush to remove any lint trapped inside the hose. Additionally, check the exterior vent cover and remove any lint or debris that may be obstructing airflow. A clear venting system promotes efficient drying and reduces the risk of overheating.
Consider Professional Dryer Vent Cleaning: For a thorough cleaning and maintenance of your dryer’s venting system, consider hiring a professional dryer vent cleaning service. These professionals have specialized tools and expertise to remove lint buildup from the entire venting pathway, including hard-to-reach areas. Professional cleaning is recommended at least once a year to ensure optimal performance and safety.
Door Issues
If you’re experiencing problems with the door of your Speed Queen dryer, it can prevent the appliance from operating properly. Here are a few common door-related issues and potential solutions:
Door Not Closing Properly: If the dryer door doesn’t close securely, it may not engage the door switch, which can prevent the dryer from starting. Ensure that there are no obstructions or debris blocking the door’s closing mechanism. Gently clean the door latch and the surrounding area to remove any dirt or lint buildup. If the problem persists, the door latch or hinge may need adjustment or replacement. Contact a professional technician for assistance.
Door Switch Malfunction: The door switch is a safety feature that stops the dryer from running when the door is open. If the switch is faulty, it may not detect when the door is closed, resulting in the dryer not turning on. Listen for a clicking sound when you close the door. If you don’t hear it, the door switch may need to be replaced. It’s advisable to seek the help of a qualified technician for this repair.
Door Stuck or Difficult to Open: If the dryer door becomes stuck or is challenging to open, it can be frustrating. First, ensure that there is no laundry or other objects obstructing the door’s movement. Check if the door hinge is loose or damaged. Lubricating the hinge with a small amount of silicone spray or applying a mild household lubricant can sometimes help resolve the issue. If the problem persists, consult a professional technician for further inspection.
- Door Seal Damage: The door seal, also known as the gasket or rubber grommet, creates an airtight seal when the door is closed. A damaged or worn-out door seal can lead to heat loss, inefficient drying, or moisture leakage. Inspect the seal for any signs of cracks, tears, or deformities. If you notice any damage, replace the door seal with a genuine Speed Queen replacement part. Refer to the user manual or contact Speed Queen customer support for guidance.
Inaccurate Timer
If you’re experiencing an inaccurate timer on your Speed Queen dryer, where the timer doesn’t accurately reflect the drying time or doesn’t advance properly, shared below are a few steps you can take to troubleshoot the issue:
strong>Check for Obstructions: Ensure that there are no obstructions or debris around the timer dial or buttons. Sometimes, dirt or lint buildup can interfere with the timer’s functionality. Clean the area around the timer carefully using a soft cloth or a gentle brush.
Inspect the Timer Knob: Examine the timer knob for any signs of damage or misalignment. If the knob is loose or doesn’t fit snugly, it may be causing inaccuracies in the timer’s operation. Try repositioning or tightening the knob to see if it improves the accuracy.
Test the Timer Functionality: Set your dryer to a specific drying time and observe if the timer counts down accurately. If it doesn’t advance or gets stuck at a particular point, it’s likely a problem with the timer mechanism. In such cases, it’s recommended to seek professional assistance from a technician or contact Speed Queen customer support for further guidance.
Consider Replacement: If the timer continues to exhibit inaccuracies even after troubleshooting, it might be necessary to replace the timer mechanism. Consult a professional technician or contact Speed Queen customer support to inquire about replacement parts and the proper installation process.
Burning Smell
If you’re experiencing an inaccurate timer on your Speed Queen dryer, where the countdown doesn’t match the actual drying time, there are a few potential causes and solutions to consider:
Check for Obstructions: First, ensure that there are no obstructions or debris around the timer knob. Sometimes, dirt or lint can get trapped and interfere with its proper functioning. Gently clean the knob and the surrounding area to remove any buildup.
Inspect the Timer Knob: Examine the timer knob itself for any visible damage or signs of wear. If the knob is loose or broken, it may not align correctly with the internal mechanism, leading to an inaccurate timer. In such cases, replacing the timer knob may be necessary. Refer to the user manual or contact Speed Queen customer support for the appropriate replacement part.
Verify the Timer Motor: The timer motor is responsible for advancing the timer mechanism throughout the drying cycle. If the motor is faulty or malfunctioning, it can result in an inaccurate timer. Contact a professional technician or Speed Queen customer support to inspect and replace the timer motor if needed.
Reset the Dryer: Performing a reset on your dryer can sometimes resolve minor electronic glitches that may cause timer inaccuracies. Unplug the dryer from the power source for a few minutes, then plug it back in. This simple reset may restore the timer’s functionality.
Professional Assistance: If the above steps do not resolve the issue, it’s advisable to seek the assistance of a professional technician. They have the expertise and tools to diagnose the problem accurately and provide the necessary repairs or replacements.
Clothes Coming Out Wrinkled
If you find that your clothes are coming out of your Speed Queen dryer wrinkled, there are a few factors to consider and steps you can take to address the issue.
Follow these troubleshooting tips to help prevent wrinkles in your laundry:
Proper Loading: Avoid overloading the dryer with too many clothes. Overcrowding can lead to inadequate airflow and cause clothes to bunch up and wrinkle. Instead, opt for smaller loads that allow garments to move freely during the drying cycle.
Sorting Clothes: Separate your laundry based on fabric type and weight. Mixing heavy items with delicate ones can lead to wrinkling. Dry similar fabrics together to ensure even drying and reduce the chances of wrinkling.
Remove Clothes Promptly: Once the drying cycle is complete, promptly remove your clothes from the dryer. Leaving them sitting in the drum can contribute to wrinkles. Shake out each garment gently before folding or hanging them to help minimize wrinkles.
Adjust Dryer Settings: Check the dryer settings to ensure you’re using the appropriate heat level and cycle for the type of fabric you’re drying. Delicate fabrics may require lower heat settings to prevent excessive wrinkling. Follow the manufacturer’s guidelines for best drying practices.
Consider Tumble Wrinkle Guard: Some Speed Queen dryers offer a “Tumble Wrinkle Guard” feature. Activate this option to periodically tumble the clothes after the drying cycle is complete, helping to prevent wrinkles from setting in if you’re unable to remove the clothes immediately.
Electrical Problems
Dealing with electrical problems in your Speed Queen dryer can be frustrating, but don’t worry. Here are a few simple troubleshooting steps to address common electrical issues:
Check the Power: Ensure that the dryer is securely plugged into a functioning power outlet. Sometimes, a loose connection can cause the dryer to lose power. Confirm that the power cord is properly inserted and hasn’t become dislodged.
Inspect the Circuit Breaker: Locate the circuit breaker panel in your home and check if the breaker for the dryer has tripped. If it has, reset the breaker by flipping it off and then back on. If the breaker keeps tripping, there may be an electrical overload or a more serious issue. Contact a professional electrician for assistance.
Test the Outlet: Use a multimeter or a simple plug-in tester to check if the outlet is receiving electrical power. If the outlet is not working, try plugging the dryer into a different outlet that you know is functioning correctly.
Check the Dryer Cord: Examine the power cord for any visible damage or frayed wires. If you notice any issues, the cord may need to be replaced. Contact Speed Queen customer support or a qualified technician for assistance.
Call a Professional: If you’ve gone through these steps and are still experiencing electrical problems with your Speed Queen dryer, it’s best to seek help from a professional technician. They have the expertise to diagnose and fix complex electrical issues safely.
Drum Not Spinning
If you’re experiencing the issue of the drum not spinning in your Speed Queen dryer, follow these simple troubleshooting steps to identify and potentially resolve the problem:
Check Power and Start Button: Ensure that the dryer is receiving power. Check that it is plugged in securely and that the circuit breaker or fuse is not tripped or blown. Press the start button firmly to ensure it is engaged properly.
Examine the Drive Belt: The drum in your dryer is typically rotated by a drive belt. Over time, the belt may become worn or broken, causing the drum to stop spinning. Open the dryer door and manually rotate the drum. If it moves freely, the drive belt may need to be replaced. Consult the user manual or contact Speed Queen customer support for guidance on replacing the drive belt.
Inspect the Drum Rollers or Glides: The drum is supported by rollers or glides that allow it to spin smoothly. If these components become worn or damaged, they can prevent the drum from spinning. Carefully access the drum rollers or glides and check for any signs of wear or damage. If necessary, replace the faulty parts following the manufacturer’s instructions.
Check the Motor: A malfunctioning motor can also cause the drum not to spin. Listen for any unusual noises coming from the dryer when you attempt to start it. If you hear a humming sound but the drum does not spin, it may indicate a motor issue. In such cases, it’s recommended to seek professional assistance from a qualified technician to diagnose and repair the motor problem.
Gas Dryer Not Igniting
If your Speed Queen gas dryer is not igniting, it can be frustrating, but there are a few troubleshooting steps you can take to address the issue. Follow these simple suggestions to get your gas dryer working again:
Check Gas Supply: Ensure that the gas supply to the dryer is turned on. Verify that the gas shutoff valve, usually located behind the dryer, is fully open. If you recently had any work done on your gas supply line, make sure the valve wasn’t accidentally closed.
Inspect Igniter: The igniter is responsible for lighting the gas in the burner assembly. Over time, it can become worn out or faulty, preventing the gas dryer from igniting. Carefully access the igniter (refer to the manufacturer’s manual for guidance) and visually inspect it. If you notice any visible cracks, breaks, or discoloration, it’s likely a sign of a faulty igniter that needs to be replaced.
Check Gas Valve Solenoids: Gas valve solenoids control the flow of gas to the burner assembly. If one or both of the solenoids are defective, the gas supply to the burner will be interrupted, causing the dryer not to ignite. Consult the manufacturer’s manual to locate the solenoids and use a multimeter to test their continuity. If the solenoids fail the continuity test, they should be replaced.
Clean Burner Assembly: A dirty or clogged burner assembly can also prevent the gas dryer from igniting. Carefully remove the burner assembly, following the manufacturer’s instructions, and clean it using a soft brush or compressed air. Be sure to remove any debris, lint, or obstructions that may be blocking the burner ports.
Check Ignition Sensor: Some gas dryers have an ignition sensor or flame sensor that detects whether the gas has ignited. If the sensor is dirty or malfunctioning, it may prevent the gas burner from staying lit. Clean the sensor using a soft cloth or mild abrasive, or replace it if necessary.
Error Codes
Encountering error codes on your Speed Queen dryer can be frustrating, but they are designed to help identify specific issues. Here’s a simple troubleshooting guide to tackle error codes:
Refer to the Manual: The first step is to consult your Speed Queen dryer’s manual. It should contain a list of error codes along with their corresponding meanings and recommended actions. Locate the error code displayed on your dryer’s control panel and cross-reference it with the manual to understand the issue.
Reset the Dryer: Sometimes, error codes can be triggered due to temporary glitches. Try resetting the dryer by unplugging it from the power source for a few minutes. Then, plug it back in and see if the error code clears. If the error persists, proceed to the next step.
Check for Obstructions: Error codes can sometimes indicate blocked airflow or obstructions within the dryer. Inspect the lint filter, exhaust vent, and any other ventilation components for debris or clogs. Clear away any buildup that may be impeding proper airflow.
Verify the Sensor Connections: Some error codes may be related to faulty sensor connections. Ensure that all the sensors are securely connected and free from damage. If you notice any loose or damaged wires, consult a professional technician to properly repair or replace them.
Contact Customer Support: If the error code persists despite your troubleshooting efforts, it’s advisable to contact Speed Queen’s customer support or seek assistance from a qualified technician. They will have the expertise to diagnose and resolve the specific error code you’re encountering.
Common Error Codes
The following are some common error codes that you may encounter on a Speed Queen dryer:
E1: This error code typically indicates a problem with the thermistor or temperature sensor. It may require a replacement or professional assistance to resolve the issue.
E2: The E2 error code usually signifies a problem with the dryer’s motor or motor relay. It’s recommended to seek professional service to diagnose and repair this issue.
E3: This error code commonly points to an issue with the dryer’s thermal fuse or thermal cutoff. These components may need to be replaced to restore normal operation.
E4: The E4 error code indicates an airflow restriction or problem with the dryer’s venting system. Check for obstructions in the exhaust vent and ensure proper airflow for efficient drying.
E5: This error code typically indicates a fault in the heating element or heating circuit. A professional technician may be required to diagnose and resolve the problem.
- E6: The E6 error code usually signifies a communication error between the dryer’s control board and other components. It’s advisable to contact Speed Queen’s customer support or a professional technician for assistance.
E7: This error code commonly indicates an issue with the dryer’s door switch or door latch. Ensure that the door is closing properly and that the switch or latch is functioning correctly.
Attention! Please note that these error codes may vary depending on the specific model and generation of your Speed Queen dryer. Refer to your dryer’s manual for a comprehensive list of error codes and their corresponding meanings.
Regular Maintenance
Performing regular maintenance on your Speed Queen dryer is essential to ensure optimal performance, prolong its lifespan, and prevent potential issues. Listed here are some important maintenance tasks to keep in mind:
Clean the Lint Filter: After every drying cycle, remove lint from the lint filter. A clogged lint filter can restrict airflow, causing longer drying times and potentially increasing the risk of fire. Simply slide out the lint filter, remove the lint, and reinstall it.
Inspect and Clean the Venting System: Regularly check the dryer’s venting system for any obstructions or buildup. Disconnect the dryer from the power source, remove the vent hose, and inspect it for lint accumulation or blockages. Clear away any lint or debris and ensure that the vent hose is securely reattached.
Clean the Interior Drum: Over time, residue from fabric softeners or dryer sheets can accumulate on the interior drum surface. Clean the drum periodically using a soft cloth and mild detergent mixed with water. Avoid using abrasive cleaners that can damage the drum’s finish.
Check and Clean the Moisture Sensor: If your dryer is equipped with a moisture sensor, it’s important to keep it clean and free from residue. Use a soft, dry cloth to wipe away any buildup on the sensor. This ensures accurate moisture detection and prevents over-drying or under-drying of your laundry.
Inspect the Power Cord: Regularly check the power cord for any signs of damage or wear. If you notice frayed wires, exposed insulation, or loose connections, contact a professional technician to safely replace the power cord.
Level the Dryer: A properly leveled dryer ensures smooth operation and prevents excessive vibration. Check that the dryer is level by using a bubble level. If adjustments are needed, follow the manufacturer’s instructions to level the appliance.
Schedule Professional Maintenance: Consider scheduling professional maintenance for your Speed Queen dryer at regular intervals. A qualified technician can inspect the dryer, clean internal components, and identify any potential issues before they escalate.
By following these maintenance tasks on a regular basis, surely you can keep your Speed Queen dryer in optimal condition, reduce the risk of malfunctions, and ensure efficient and reliable drying performance.
Conclusion
In conclusion, we hope that this Speed Queen Dryer Troubleshooting Guide has provided you with valuable insights and practical solutions to address common issues with your dryer.
By following the troubleshooting steps outlined in this guide and performing regular maintenance, certainly you can enhance the performance, efficiency, and longevity of your Speed Queen dryer.
Remember to always prioritize safety and, if needed, consult a professional technician for complex repairs. Enjoy hassle-free drying and the convenience that your Speed Queen dryer brings to your laundry routine.
Note: You can read other “Appliance Troubleshooting Guides” here.
Other Appliance Troubleshooting Guides:
- Maytag Washer Troubleshooting: Quick Fixes for Problems
- Expert Tips for Whirlpool Washer Troubleshooting Guide
- How to Fix Frigidaire Glass Top Stove Oven Not Working